气缸油使用管理
2022-05-18 来源:润滑油情报
摘要:气缸油除要满足气缸套、活塞和活塞环之间的润滑和密封要求,之外还要承受有强烈腐蚀性的高温、高压周期性变化的燃气冲刷。
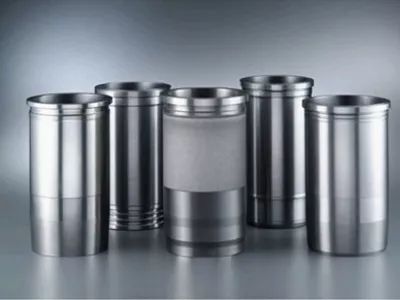
在柴油机各运动部件的润滑中,以气缸油的工作条件最为严酷。首先,气缸油除要满足气缸套、活塞和活塞环之间的润滑和密封要求,之外还要承受有强烈腐蚀性的高温、高压周期性变化的燃气冲刷。
随着燃油质量的劣化,所含腐蚀性燃气成分的比重也呈上升趋势,这对气缸的腐蚀也更加剧烈,相应地要求气缸油必须具有足够的碱值,及时中和这些燃油燃烧中所产生的酸性物质。因此,要求气缸油的抗氧化、抗腐蚀性能也在逐渐提高。
任何事物都具有两面性,性能优越、高黏度和高碱值的气缸油,对于使用管理要求也相应提高,使用不当就会使气缸内结垢增加,运动部件磨损加剧。据统计,在气缸磨损事故中,约有50%以上是由管理不当所造成的。
一、气缸套的正常磨损
柴油机的技术状态和使用寿命很大程度上取决于气缸套的磨损情况。在正常工作条件下气缸套磨损是不可避免的。一般只要气缸套的磨损量在允许范围之内(最大允许磨损量 为 0.4%~0.8%缸套内径),气缸套就处于正常工作状态。
1、气缸套正常磨损的标记
气缸套正常运转工况下正常磨损的特征是最大磨损部位在气缸套上部,即活塞位于上止点时第1、2道活塞环对应的缸壁处,并沿缸壁向下磨损量逐渐减小,气缸内孔呈喇叭状。气缸套左右舷方向的磨损大于首尾方向的磨损。
磨损的正常参数:圆度误差、圆柱度误差、内径增量(缸径最大增量)小于说明书或有关标准的规定值;缸套磨损率:铸铁缸套<0.1 mm/kh,镀铬缸套在0.01~0.03 mm/kh;气缸工作表面清洁光滑,无明显划痕、擦伤等磨损痕迹。
2、正常磨损的原因
1)处于边界润滑部位的局部金属直接接触引起的粘着磨损。或因过薄的油膜被工作表面的尖锋刺破,或因高温、速度低等使油膜未能形成或遭破坏。
2)进入气缸的新鲜空气中的灰尘,燃油或滑油燃烧生成的各种氧化物、炭粒和灰分,润滑油中的机械杂质及运动副的摩擦产物等均会引起磨粒磨损,且以气缸上部最为严重。
3)燃油中硫分的燃烧产物对缸壁的硫酸腐蚀。由于活塞在上止点时第1道环对应缸壁处含酸量最大,为缸套下部的4倍,造成缸套上部严重的腐蚀磨损。气缸上部燃气温度与压力对硫酸露点的影响,使上部凝结较多的酸。
二、气缸套的异常磨损
1、异常磨损的特征
1)气缸套和活塞环的磨损率均很高,大大超过正常磨损率。一般铸铁缸套磨损率>0.1 mm/kh,活塞环磨损率>0.5 mm/kh。
2)缸套工作表面脏污,有明显的划痕、擦伤、撕裂等拉缸和咬缸现象,或者缸壁表面发蓝,有明显的烧灼现象。缸套工作表面形貌和金相组织发生变化。
3)异常磨损的磨损产物颗粒较大。一般正常磨损的磨屑直径<1 μm,而异常磨损的磨屑直径达25~30 μm。
4)气缸套异常磨损在吊缸检修时可以直观判断,或通过测量缸径计算出的磨损率、内径增量(或圆柱度误差)和圆度误差等来判断。
2、异常磨损的原因
船舶航行期间,柴油机气缸套发生异常磨损主要是工作中的问题引起,在分析原因 时应首先分析工作参数和维护管理工作对磨损的影响,这是研究问题的起点,解决问题的方向。
1)燃油和燃烧的质量
燃油中的含硫量是气缸套产生腐蚀磨损的重要原因,燃油中含硫量超过 0.7%~1.0% 时,磨损急剧增加。因为含硫量增加使硫酸凝结温度(即露点)升高,在气缸工作条件下容易发生腐蚀。含硫量高的燃油燃烧时生成较多的炭粒,并促进积炭的形成,加重磨粒磨损。燃油中灰分含量高时,燃烧后生成金属氧化物或金属盐,增加缸套的磨粒磨损。
船用低速柴油机燃用低质燃料油对缸套的磨损较燃用低硫柴油高2~3倍。燃料油中未清除掉的极硬的硅酸铝颗粒,严重增加了缸套的磨粒磨损。燃油燃烧不良,如燃烧不完全、后燃等均会使炭粒增加,磨损加重。
2)冷却水温的管理
气缸套冷却水温控制不佳会使缸套磨损增加。一般来说冷却水出口温度过低,使缸壁温度过低,硫酸腐蚀加重;冷却水出口温度过高,缸壁冷却不良,温度较高,致使缸壁上油膜蒸发,滑油氧化,积炭严重,导致粘着磨损。同时,缸壁温度过高不仅热负荷增加还影响活塞环的散热,使环的磨损加重。
实践证明,适当提高缸套冷却水出口温度,使缸套表面温度高于露点,可有效地防止 腐蚀,减少磨损。一般出口温度控制在 85℃~95℃时缸套磨损量较小。
3)润滑油的管理
活塞环与缸套工作表面间的边界油膜极薄,它有赖于润滑油中极性团的物质。合适的润滑油或含有极性添加剂的润滑油能够形成承受较高负荷的边界油膜。润滑油的其他品质,如抗氧化安定性、残炭值等也利于气缸润滑。柴油机燃用低质燃油时,气缸油的碱值应与其匹配,以中和燃油燃烧时产生的酸,有效地降低腐蚀磨损。
因此,润滑油品质不良或不适,碱值不当或轮机员对润滑油管理、使用不善,如油压不足、断油、长期使用不化验、不更换以致滑油变质等,均会引起缸套异常磨损。