水性防锈剂研究与应用现状
2022-04-28 来源:润滑油情报
摘要:根据水性防锈剂的应用实践,金属加工行业对于工件加工后的表面要求越来越高,无论是水性防锈剂单独使用,还是添加到其他水性金属加工液中使用,均要求使用后工件表面不能有肉眼可见残留,且不能影响后道加工
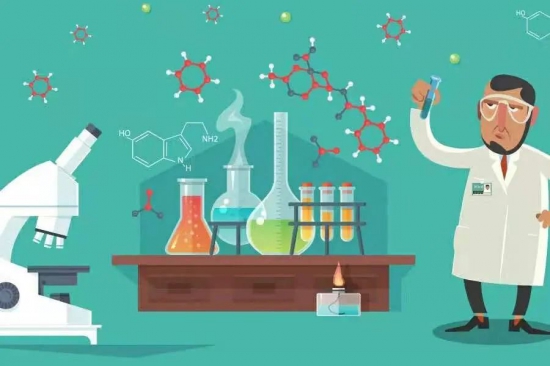
目前金属加工行业内常用的防锈材料主要分为以下几类 :
(1)无机类的,主要有亚硝酸钠、钼酸盐、硼酸盐等,其中亚硝酸盐和钼酸盐属于氧化性防锈剂,但形成的防锈膜层并不是非常致密,需要一些成膜剂辅助。
(2)有机类的,主要有醇胺、羧酸盐(以一元酸、二元酸和三元酸为主)、硼酸酯、酰胺等,该类防锈材料在不同行业均会有所应用。其中羧酸类是应用最广泛的一类防锈添加剂,使用前需要与不同类型的醇胺中和成羧酸胺使用,但该类防锈剂成本较高。硼酸酯类防锈剂不仅具有较好的抗迭印效果,还具有一定的抗菌能力,但这类防锈剂不够稳定,有水解的可能性。
(3)成膜助剂,目前报道较多的是聚乙二醇、聚丙烯酸钠、水溶性树脂等,有人曾做过试验验证,PEG1500 比 PEG400 具有更好的成膜效果。
低残留水性防锈剂研究的专利现状
根据水性防锈剂的应用实践,金属加工行业对于工件加工后的表面要求越来越高,无论是水性防锈剂单独使用,还是添加到其他水性金属加工液中使用,均要求使用后工件表面不能有肉眼可见残留(包括白色残留、固体颗粒物、软粘性残留等),且不能影响后道加工,如装配、焊接等。因此,针对低残留水性防锈剂的研究,已成为众多行业内从业者的研究对象之一,目前已经公开、审查或授权的研究成果或研究进展详见下表 1。
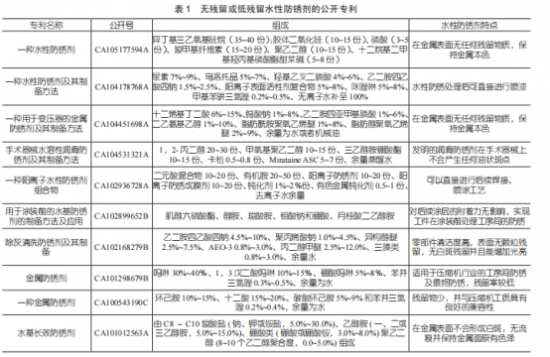
由表 1 可知,低残留水性防锈剂的特点是主要采用有机物作为主防锈剂,如羧酸盐、醇胺、硼酸、硼酸酯、硅烷等,同时添加一些成膜助剂增强成膜效果,如聚丙烯酸钠和聚乙二醇,考虑到润湿性和渗透性,成膜助剂也可以是一些表面活性剂或醇醚溶剂,可选用的表活主要是阳离子表面活性剂和非离子表面活性剂。其中,阳离子表面活性剂吸附在金属表面后,烷基链暴露在空气中具有一定的疏水效果,有助于隔离潮湿空气,并保持自清洁功能,将是水性金属防锈剂的一个重要研究方向。
水性防锈剂应用现状
热处理行业常见的生锈问题是回火后生锈、回火后放置过程中生锈或回火并抛丸后生锈,极端情况下淬火清洗后就会出现生锈。目前行业内越来越多的客户开始使用环保型水性防锈剂,淬火后用水性清洗剂清洗并用水性防锈剂漂洗,但这类防锈剂有个缺点,由于有效防锈成分主要是有机物,在进行高温回火后会产生一定的高温分解,降低防锈效果,但对于低温回火则影响不大。也有部分企业仍然使用传统的无机型防锈剂,以亚硝酸钠作为主要防锈成分,此类防锈剂在防锈效果方面很突出,但容易在工件表面产生结晶,甚至吸潮,影响外观。也有客户使用乳化型防锈剂,具有较好的抗湿热效果和一定的抗盐雾能力。
在金属工件机加工过程中,工序间防锈主要以水性防锈剂为主,而储存防锈和长期防锈则以防锈油为主。水性防锈剂相比防锈油,具有很好的可清洗性,尤其是在金属加工的工序间防锈,进入下道加工前很容易被去除,或者可直接进行加工,同时,水性防锈剂一般与切削液、磨削液、清洗剂等其他水性加工介质均具有较好的相容性。
目前,此类防锈剂主要以羧酸和胺类作为主要防锈成分,并与酰胺、硼酸盐、表面活性剂、其他成膜助剂等进行复配,起到协同防锈的效果,如果是多种材质防锈,还需添加一些有色金属缓蚀剂。受到企业规模和经营范围、地理位置、地方法规要求等因素影响,各企业对于水性防锈材料的选择标准也有所不同,总体来讲,随着更多企业的环保健康意识在逐步增强,会优先选择使用绿色环保的水性防锈剂。但仍然有部分企业,在使用具有潜在健康危害的防锈剂组分,主要是基于成本方面考虑,也有部分原因是为了满足企业自身对于防锈时间的期望。
为了加强水溶性工业介质类产品的防锈性能,也可将水性防锈剂加入到其他水性产品中以增强防锈能力。为了降低使用风险,体验更好的服务,水性防锈剂使用企业一般会针对上下道工序选择同一家介质供应商,一方面是因为介质间的相容性更好,另一方面是可获得整体解决方案。