刀具制造与磨削油液使用
2021-07-12 来源:润滑油情报网
摘要:为了适应加工的高精度化、高速化、自动化、多功能化和高生产率化,切削刀具要求有更高的强度和韧性,并具备长寿命、高可靠性、耐高温、耐磨损、抗氧化和抗冲击等特点。这对于切削刀具的设计和制造以及金属加工液产品的研发和应用提出了新的要求。
为了适应加工的高精度化、高速化、自动化、多功能化和高生产率化,切削刀具要求有更高的强度和韧性,并具备长寿命、高可靠性、耐高温、耐磨损、抗氧化和抗冲击等特点。这对于切削刀具的设计和制造以及金属加工液产品的研发和应用提出了新的要求。
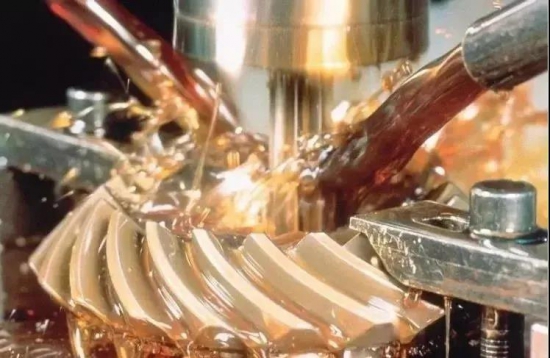
硬质合金刀具及其特点
目前各类刀具中应用最多的是硬质合金刀具。所谓硬质合金,即由碳化物(主要为碳化钨WC、碳化钛TiC、碳化钽TaC和碳化铌NbC)与金属黏接剂钴通过粉末冶金制成的合金。
由于硬质合金刀具材料本身硬度高,脆性大,导热系数小,因而给刀具的刃磨,尤其是磨削余量较大的整体硬质合金刀具的刃磨带来很大困难。其中包括:①刀具材料硬度高,要求有较大的磨削压力;②刀具材料导热系数低,不允许产生过大的磨削热量;③刀具材料脆性大,导致产生裂纹的可能性增大。
磨削油液选用
对于刀具制造商来说,在刀具制造过程中,除了需要考虑设备、砂轮等因素,还有一个不可忽视的问题,就是合理选择磨削液与磨削油。
(1)磨削液的选择。硬质合金材料本身硬度较高且脆性较大,磨削加工温度可达1 000 ℃左右,但产生的大量热量中只有15%随磨屑带走,8%随工件带走。
对于应用于硬质合金刀具制造的磨削液,其应具备性能特点如下:
①较好的润滑性能、极压性能;
②优异的冷却性能,可以及时冲走磨削产生的磨屑和砂轮磨损的砂粒;
③较好的抗泡性,有效保证冷却性和清洗性;
④有效防止钴的析出。
(2)磨削油的选择。与磨削液相反,使用磨削油的首要目的不是为切削区域降温,而是通过提供高润滑性来减少热量的产生。
通常对应用于硬质合金刀具制造的磨削油的要求如下:
①采用具有更高闪点和更低蒸发性的品质较好的基础油,这样在同等黏度条件下,可大大减少油品损耗,提高工作环境的整洁程度。
②磨削油具有合适的黏度,保证油品有优良的冲洗性能和沉降性能。
③磨削油采用合理的配方体系,如避免使用含硫和氯的极压添加剂,防止磨削油对机床有色金属部件产生腐蚀。
使用磨削油时的硬质合金刀具磨削加工现场如图2所示。使用磨削油时的硬质合金钻头磨削加工现场如图3所示。
目前刀具磨削的关键设备均是五轴磨床,但必须强调的是,磨削油/液的正确使用对于保证设备的生产效率非常重要。由于砂轮在高速高温磨削中急剧升温,热量很难快速散出。只有依靠合适的磨削油/液才能够让磨削温度保持在正常工作范围内,从而降低砂轮损耗,延长使用寿命,同时保证刀具的质量。
部分客户为了“节约成本”而使用普通磨削油/液进行冷却,这不仅会使磨削过程中产生大量烟雾,还会影响刀具质量,并极大地缩短砂轮寿命,这是不可取的,客户应根据砂轮类型、加工尺寸等因素来选择合适的磨削油/液。