润滑油矿物基础油的生产现状及发展方向将如何?
2021-07-08 来源:润滑油情报网 网友评论 0 条
摘要:随着润滑油需求量的增大,对润滑油基础油生产技术改进工作更加重视,实现生产成效的持续改进。但实际上我国润滑油矿物基础油的生产工艺形式相对固化,技术革新的步伐整体滞后,与国外先进国家相比仍有较大的发展距离。
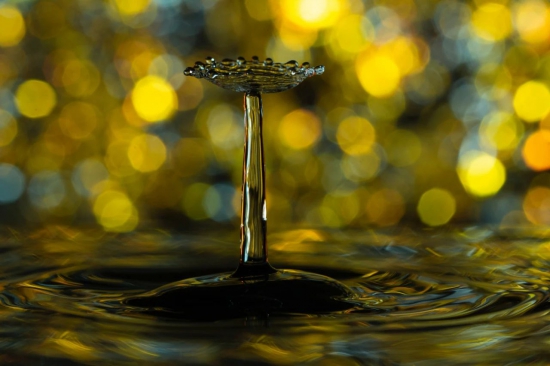
润滑油是机械运转必须的润滑剂,主要作用是减轻机械运动部件之间的磨擦与磨损。生产润滑油的主体成分为基础油,按原料来源分类基础油主要分为矿物基础油、合成基础油以及植物油基础油三类。其中,矿物基础油来源于石油的炼制过程,应用最为广泛,用量占比在 90% 以上。
润滑油基础油在市场环境变化与是企业发展压力等因素影响,传统润滑油矿物基础油的生产工艺,俨然不能满足企业现代化的发展要求,还需加大对生产工艺的优化力度,改进工艺流程的同时,降低生产成本,提高产品的质量与效益。
润滑油矿物基础油的生产现状
矿物基础油由原油提炼而成。主要生产过程有:常减压蒸馏、溶剂脱沥青、溶剂精制、溶剂脱蜡、白土或加氢补充精制。矿物基础油的化学成分包括高沸点、高分子量烃类和非烃类混合物。现代科技加速了传统基础油生产工艺的改革进程,尤其是加氢工艺,作为基础油生产的核心技术,可提高产品的性能与品质,在润滑油基础油制造行业的应用越发成熟与自如。
随着润滑油需求量的增大,对润滑油基础油生产技术改进工作更加重视,实现生产成效的持续改进。但实际上我国润滑油矿物基础油的生产工艺形式相对固化,技术革新的步伐整体滞后,与国外先进国家相比仍有较大的发展距离,尤其是终端与高端的矿物基础油制造技术尚未完全摆脱对进口的依赖,自主生产的研发维度相对不足。与此同时,节能环保与降耗等生产政策的颁布,对润滑油矿物基础油生产工艺技术的改革提出了更高要求,为提高生产工艺与产品需求及生产政策号召等方面的匹配度,加大技术改革的研究力度显得尤为重要。

润滑油矿物基础油的生产工艺及优化
(1) 常减压蒸馏
常减压蒸馏生产工艺,是指在减压与常压作用下,通过精馏 手段,围绕各组分的挥发度,汽液两相在塔盘上多次逆向接触, 多次进行部分汽化与部分冷凝,从而分离出原油中的柴油与汽 油及煤油。
(2) 丙烷脱沥青
基于特定温度下丙烷对减压渣油中润滑油及蜡的溶解能 力较大,但对沥青质与胶质无溶解能力的原理,可有效去除减压渣油中的沥青质与胶质,可同时生产出润滑油与沥青。
(3) 溶剂精制
基于特定温度下溶剂中的活性极性分子可溶解的原理,可 有效溶解与分离出润滑油中的非理想成分,从而调整油品粘温 性能,降低酸值与残炭值,提升油品的安定性。在分离物中蒸馏出溶剂可得到抽出油,从而为车轴油调和提供抽出油原料,溶 剂主要以酚或丙烷等物质为主。
(4)加氢处理
在压力与氢气及催化剂等条件下,通过加氢处理,可将原 料中的沥青质等不理想分子,通过加氢裂解反应转变为有益组分,促使精油品黏指数与润滑油精制度显著提高。加氢工艺线 路包括加氢组合传统工艺与全加氢工艺两种,加氢技术生产出来的基础油,可增强原料的适应性,扩大润滑油料的范围,提高基础油的质量。加氢工艺生产基础油有较高的副产品附加值,生产效率相对较高。但基础油的产品质量不尽理想,与进口产品相比存在明显的质量差距,究其原因认为与装置的开工率低等因素影响有关,因此可通过提高开工率与积累操作经验等措施处理质量问题。
如日本三菱公司研发的燃料型加氢裂化-溶剂精制-溶剂脱蜡-加氢后精制的技术线路,实现了传统润滑油精制装置工艺与加氢裂化装置工艺的结合,在生产低等与中等黏度的超高黏度指数基础油时,加入软蜡更利于生产工艺的有序展开。加氢工艺过程中的化学反应,主要包括杂环化合物脱除;正构烷烃或低分支异构烷烃临氢异构化为高分支异构烷烃;芳烃饱和、环烷烃开环及异构化。通过对产生轻油的反应进行抑制,可有效提高基础油的收率与黏度指数。联合加氢处理与脱酸工艺,更适用于生产环烷基润滑油,同时可有效解决原油酸值较高的问题。
(5) 白土精制
白土经过盐酸处理后的活性与吸附力及选择性增强。从操作方式入手分析,主要将油与白土在特定温度下混合,利用白土的吸附能力与各种工序,将基础油中的折氮化物与沥青质等杂质去除,从而改善基础油的颜色,促使其残炭量与碱氨含量降低,抗氧化安定性与油品的稳定性显著提高。白土补充精制工艺可有效脱除有品种的残余溶剂,以及含硫与氮的极性化合物。但工艺中运用到的白土用量较大,且粉尘污染与精制油损失较大等问题不能忽视。
我国基础油的含氮量相对较高,降低了基础油的氧化安定性,利用脱氮 - 白土联合工艺,可有效解决碱性氮含量高的问题,同时降低白土的用量。随后生产出来的络合脱氮 - 白土联合装置,可显著提高产品质量,装置收率与白土的用量及,精制油旋转氧弹指标等方面均得到了有效的优化。废白土量的减少,也解决了粉尘污染的环境问题。随后生产出来的无白土工艺,即利用低温高效吸附剂取代白土,如BLS-X100 型吸附剂的应用,可有效解决油品损失与白土污染及装置降耗等问题,生产成本降低,设备使用周期延长,更利于提高效益价值。
(6)脱蜡
在基础油的生产过程中,为改善油品的低温流动性,可围绕原油中的含蜡量与油料质量的不同要求进行脱蜡操作。蜡可溶解于油,溶解度与温度变化有密切关系。当油中的蜡处于饱和状态时会析出晶体。结晶随着温度的降低为增大,再通过过滤工序分离出蜡和油,从而完成结晶脱蜡的过程。结晶脱蜡程序相对复杂,涉及溶剂脱蜡与冷榨脱蜡等,应用溶剂脱蜡程序时,随着温度的降低,需加入有选择性溶解力的溶剂,对油的溶解力较强,对蜡的溶解力弱,最后通过过滤实现蜡和油分离。溶剂有溶解油与降低油品黏度及促使蜡形成结晶、降低过滤阻力等作用,可将蜡轻易分离出来。
从异构脱蜡入手分析,异构脱蜡过程是指将烷氢异构分子分为单链异构,通过不断的分解分子,提高油品的制作质量。异构脱蜡方法弥补了催化脱蜡中基础油倾点变化对油品黏度及收率影响的不足,从而在工业化生产中的应用范围更广。异构脱蜡技术的优势特征明显,包括基础油的热稳定好与蒸发损失小及高黏度指数等方面,相比较于传统的原料处理工艺,基础油生产工艺的收率与副产品值更高。
从催化脱蜡入手分析,催化脱蜡技术可在临氢状态下促使油品分子裂化,减少基础油的凝固点。当利用中间基油与轻质石蜡基油为原料时,黏度指数会随着基础油的凝固点下降而降低。催化脱蜡技术生产的产品杂质与倾点更低,同时氧化安定好,更适用于生产中间基光亮油与环烷基等产品。
润滑油矿物基础油的发展方向
全球润滑油基础油市场处于供大于求状态的供应形势,各种结构矛盾的问题并存。随着常规基础油需求量的不断降低,非常规基础油需求量的提高,受生产技术等因素限制,难以满足供应量的问题。因此未来润滑油发展动力,主要以降低系统成本与环境无污染等方面为主。
首先从降低系统成本的角度分析,可通过延长换油时间与减少设备操作费用等途径降低成本。其次从工作条件的要求入手分析,需达到环境无污染与安全生产等要求。除此之外,未来发展还需满足高黏度与低挥发及低硫无硫等要求,满足当下应用基础油看重的低温流动性与剪切安定性及抗氧化安定性等特征,而常规基础油根本达不到要求,即使通过改变添加剂的种类与添加量的方法,也难以符合应用标准,只有使用其他类基础油才能满足应用要求。
因此合成化技术与异构脱蜡凭借较高的匹配度,逐渐成为了润滑油加工工艺的主流技术,发现空间巨大且前景良好,生产出的润滑油种类更加丰富,可拓展其应用的领域,促使其作用价值得到充分的体现。传统的溶剂精制 - 溶剂脱蜡工艺技术,适用于生产常规的润滑油基础油,为满足润滑油更新换代的要求,加大了生产不同类基础油的工艺研究力度。尤其是在加氢工艺方面,研发出了加氢改质联合溶剂脱蜡、异构脱蜡等生产技术,原料来源途径拓宽,工艺技术得到改进,油品收率与质量提高,生产成本降低。不断利用更高效的工艺与催化剂技术生产各类矿物基础油,能够促使世界润滑油生产的继续扩能与升级,将使世界润滑油市场走向新的平衡。
在汽车及工程机械日益发展,保有量日渐增多的形势下,矿物基础油仍然以性价比优势占据润滑油生产市场的主流位置。随着油品的更新换代,对多种基础油的需求逐渐提高,对基础油的黏度指数及抗氧化安定性等性能提出了更高要求,传统工艺生产出的常规矿物基础油俨然已越来越不能满足市场需求,还需采取先进的生产工艺,生产各类优质基础油,并不断通过生产工艺的优化升级,夯实矿物基础油发展的基石,促进市场的持续稳定。在生产技术改革中应当注重现代化技术的引入,拓展技术革新的路径,以尽快实现生产效益目标。
相关文章
[错误报告] [推荐] [收藏] [打印] [关闭] [返回顶部]