How Do Metalworking Fluids Work?
2012-06-28 来源:润滑油情报网
Metalworking fluid capabilities have evolved significantly over the past few decades. Unfortunately, scientific understanding of them has not kept pace.
In an effort to bridge the knowledge gap, the European Research Council has funded a project at the Foundation Institute of Materials Science (lWT) in
According to Koch, “The distinguishing feature of the CoolArt approach will be its cross-disciplinary nature. This requires a multidisciplinary research team from chemistry, physics, microbiology, mechanical engineering and materials science.”
Progress in the Dark
Today’s metalworking fluids often consist of several dozen chemical components, and formulators may have only limited knowledge of how they work and interact with machined surfaces and one another. In addition, some of these components exhibit harmful properties that pose a potential hazard to the operator and the environment.
“In recent years, metalworking fluids and their use have developed very fast,” stated Koch, a professor in IWT’s Manufacturing Technologies Division. “The rapid progress was based mainly on end-user needs rather than scientific development.” The result is a stepwise enhancement of MWF properties. However, this development was mainly performed without investigating the reasons for improvement and what side-effects accompanied the development.
The need for a deeper understanding of MWF properties has been intensified by regulations such as the European union ’s REACh (Registration, Evaluation. Authorization and Restriction of Chemicals), which creates new challenges for formulators and end-users alike. As a result of these developments, the ERC determined that a scientific study of MWFs in European industries and their effects on the environment was worthy of a grant. “The Advanced Investigator Grant allows for a holistic approach to scientifically reveal the working mechanisms in MWF composition and application,” said Koch. “The project’s name, CoolArt, derives from the goal to improve MWF functions like cooling and lubrication far beyond the current state of the art as well as increasing the fundamental knowledge about MWF working mechanisms.” The project has four phases:
• scientific investigation into MWF fundamentals to provide a better understanding of their chemical, physical and biological working mechanisms;
• detailed scientific understanding of MWF components and their interactions to allow for a reassessment of today’s fluids and pave the way for a new MWF design;
• consideration of unusual ideas such as incorporating new functions into MWFs or developing an easy-to-use system for fluid maintenance and supply;
• verification and knowledge transfer to disseminate the findings.
The project is funded for five years, and a multidisciplinary team of engineers, chemists, biologists and physicists will collaborate at IWT Bremen and with MWF producers and end-users.
Learning Fundamentals
An essential first step in the CoolArt project is to understand MWF fundamentals. Hence, IWT will focus on the chemical, physical and biological basics and review the mechanisms by which fluids, machine tools and work pieces form surface layers. As Koch noted, “Today’s fluids consist of up to 60 components, each performing a specific function, but neither the fate of a single component during the fluid’s life nor the side-effects of the fluid’s complex composition are presently known.”
The numerous components of MWFs have to be identified and investigated by chemical analysis to determine their intrinsic and extrinsic effects. “Though the initial composition is known,” said Koch, “the by-products of biological and chemical reactions over time are not. In addition, these substances are suspected to have a considerable hazard potential.”
The reactions between MWFs and the workpiece will first be studied with simple scratch tests. Careful analysis of the metal surface will help verify current theories about the working mechanisms of additives. In addition, simulation of physical properties such as fluid dynamics or heat transfer must be developed. “Also,” Koch added, “simulations of the interactions between fluid, tool and [work piece] surface on a molecular scale will provide a better understanding of the physical impact on the machining process.”
One aspect of MWFs yet to be investigated in depth is the influence of microbes on fluid service life, on the machined surfaces and on fluid performance. It is known that microbes or their metabolites foul the fluid and can clog filters and pipes. Koch said that “for the first time, this assessment will investigate the complete fluid system – including machines, storage tanks, pipes and so on – to determine how microbial populations develop over time, which bacteria or fungi are found in this environment, and what kinds of metabolic reactions cause the adverse effects.”
The identification and quantification of microorganisms in MWFs and their development over time will be performed by various state-of-theart techniques. Besides conventional methods such as counting colony forming units (CFU) or use of dip slides, the MALDI-ToF (Matrix Assisted Laser Desorption Ionization Time of Flight) technique will be used to determine specific species.
According to Koch, “Initial experiments have revealed many microorganisms that were not known to develop in MWFs.” A comprehensive understanding of chemical, physical and microbial fundamentals will be critical for a scientifically based improvement of MWFs that will be the focus of the next segment of the program.
Designing New Fluids
Results of the first phases of the project will be used to:
• design CoolArt MWFs with improved performance and sustainability;
• expand functionality by adding completely new properties to MWFs.
“Based on scientific understanding, it will be possible to develop superior fluids with fewer components, less hazard potential and increased sustainability and performance,” said Koch. “Alternative chemical, physical or microbial interactions could pave the way for yet unknown possibilities to significantly increase a fluid’s machining efficiency.”
He went on to add that new approaches, such as the development of bio-based MWFs, will challenge conventional formulation practices. Reconsidering the type of media used for MWFs has an enormous potential. “For example,” he said, “wax-like media show advantages in storage and disposal.”
In addition to improved performance and increased sustainability, completely new effects are expected to be discovered. “The expansion of fluid functionality might allow for the implementation of supplementary processes like coating or surface hardening and therefore carries a huge potential for shortening processing times and reducing costs,” Koch noted. “Another function might be the ability to react to changes in physical or chemical properties by emitting indicators that can be recognized by appropriate monitoring systems so that corrective action can be taken.”
The third segment of the study will be to simplify maintenance and develop a monitoring and adaptation system. The goal of this system will be to optimize fluid supply throughout a machining process. To be successful, Koch said, “a system combining automated maintenance and on-line adaptation should be as easy to use as plug-and-play devices for a home computer.” This would completely change the method of applying MWFs; therefore, this mission is called “Plug and Produce.”
Simplifying fluid maintenance aims at developing a system that:
• reacts to changes in properties
that impact performance (such as
microbial state or additive con- centration) by activating chemical indicators that can be detected by sensors;
• develops actuators that respond to the sensor signals to trigger actions that ensure consistent fluid quality over its expected service life.
Part of this system will be an on-demand additive supply system with sensors adapted from nature, such as an electronic nose or tongue to allow online monitoring of the fluid’s chemical state, as well as a reservoir of components to be released when needed. “Another important consideration,” said Koch, “is a supply system able to respond to the demands of the machining process.” The system would monitor physical conditions (such as process forces and temperature) to deduce the fluid’s supplemental additive requirements. Combining the monitoring system with one that can adjust flow rate, the shape and direction of nozzles or filter pore size will help maintain optimum machining conditions at all times. “Taking into account that neither an intelligent supply adaptation system nor an on-demand additive supply system exists today, the high potential for innovation from this phase becomes obvious,” said Koch.
Disseminating to Industry
“Experience shows that the advantages of new technologies are often diminished by insufficient implementation,” said Koch. “Consequently, knowledge transfer and the long-term verification of the whole project are indispensable.” Therefore, the final phase of the project has two major objectives:
• transfer of CoolArt findings to academia and industry;
• building a CoolArt demonstration facility at IWT Bremen, housing machine tools for the long-term verification of the project’s achievements, and knowledge transfer to the target groups.
The findings of the CoolArt project will be presented to academia, industry management and students. “In addition to interactive workshops for end-users,” Koch added, “project findings will be shared with national and international universities to teach new students entering the field.”
What’s more, the results of the previous phases will be verified in real-world systems. To accomplish this, machine tools will be installed in a verification area of the demonstration facility.
Koch concluded by saying, “The success of the CoolArt project relies on the cooperation of and communication with representatives of the MWF industry, including fluid producers, tool and machine tool manufacturers as well as end-users, researchers and research institutions. The results of the project are not meant to disappear into a report but to be put into practice. Therefore, a means has been established whereby industry can participate in the CoolArt project by submitting questions, expressing needs and, if they wish, offering their know-how.”
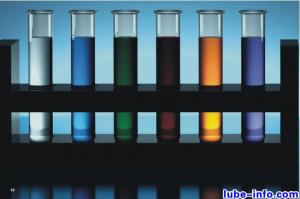